Share
Pin
Tweet
Send
Share
Send
물론, 수동 작업으로도 숙련 된 그라인더는 어렵지 않습니다. 다른 사람이 필요한 선명 각도를 쉽게 견딜 수는 없습니다. 무딘 나이프의 문제가 여전히 해결 불가능한가?

이 곤경에서 벗어날 수있는 세 가지 방법이 있습니다. 칼을 갈아 익히는 법을 배우는 데는 많은 시간과 인내와 노력이 필요합니다. 매번 전문가에게 도움을 요청하고 그의 비싼 서비스 비용을 지불하십시오. 나이프 샤프너 자체를 만들고 샤프닝 각도를 생각하지 마십시오.
아래에서는 두 개의 연마 휠이있는 전기 깎이를 기반으로 나이프를 연마하는 장치를 제조하는 방법을 고려합니다.
필요합니다
작업에 많은 시간과 에너지가 걸리지 않기 때문에 용접 기계, 기계 (드릴링, 밀링 및 터닝), 진자 톱, 드릴, 그라인더, 렌치, 마킹 도구 등의 재고가있는 것이 좋습니다.
재료 및 구성 요소에서 이미 언급 한 전기 샤프너 외에도 다음을 구입해야합니다.
- 10 mm 두께의 금속 시트;
- 정사각형 튜브 (인접한 크기의 두 조각);
- 최대 400 mm 길이 및 15-20 mm 직경의 원형 금속 막대;
- 나사산 패스너 (볼트, 너트, 와셔) 등
나이프 샤프너 만들기
이 작업은 비교적 독립적 인 두 단계로 구성됩니다 : 전기 샤프너의 배열과 필요한 샤프닝 각도를 제공하는 나이프 홀더의 제조.
샤프너 배열
나이프의 고품질 샤프닝에 필요한 조건 중 하나는 연삭 공구의 안정성입니다. 따라서, 우리는 전기 깎이의 기초로 크기와 두께에 적합한 금속 시트를 사용합니다.

줄자, 코어 및 해머를 사용하여 전기 숫돌 판의 구멍을 반복하여 네 구멍의 중심을 표시합니다. 드릴링 머신의 표시에 따라 구멍을 뚫고 볼트와 너트를 사용하여 전기 깎이를 금속베이스에 고정시킵니다.

우리는 진자 톱으로 길이를 따라 이전에 계산 된 두 개의 사각형 파이프를 잘라 냈습니다. 또한 하나는 자유롭게해야하지만 큰 간격이 없으면 다른 하나는 들어가야합니다.

더 작은 단면의 파이프에서 관통 구멍은 한쪽 끝에서 밀링되며 그 직경은 금속 막대의 직경보다 약간 커야합니다. 두 번째 파이프에서는 잠금 볼트 구멍을 한쪽 끝에서 계획하고 뚫습니다.

우리는 고정 볼트가 바깥 쪽을 향하고 상단에있는 위치에서 고정 깎이 반대편의 중앙에 큰 단면의 파이프를 바닥에 용접합니다. 용탕, 스파크 및 스케일의 용접으로 인한 전기 모터 손상을 방지하기 위해 용접 담요로 덮습니다.

우리는 막대를 중간에 엄격하게 작은 단면의 파이프에있는 드릴 구멍에 삽입 하고이 위치에서 파이프에 용접 하여이 결합 부품의 직각도를 직각 삼각형으로 확인했습니다.


이 작업을 미리 수행하지 않은 경우 전기 샤프너를베이스에서 제거하고 전기 박스를 수정 한 다음 샤프너를 제자리에 다시 설치하고 작동 상태를 확인하십시오.
우리는 막대가있는 파이프를베이스에 용접 된 파이프에 삽입하고 볼트를 사용하여 특정 나이프를 연마하는 데 필요한 높이를 설정할 수 있습니다. 이것은 전기 샤프너를 배치하는 마지막 단계였습니다. 작업의 두 번째 단계로 이동


전기 깎이에 회전 방향을 변경합니다.

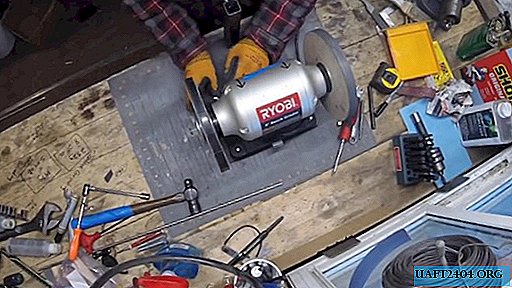
나이프 홀더 만들기
이미 언급했듯이, 나이프 샤프닝의 품질은 우선 샤프닝 각도의 불변성을 보장하는 데 달려 있습니다. 우리가 만들 홀더는 바로 이것입니다.
우리는 세 가지 요소의 의도 된 치수에 따라 금속 가공물을 표시합니다.이를 통해 날카롭게 할 때 원의 표면에 주어진 각도로 나이프 블레이드를 안전하게 캡처 할 수 있습니다.

우리는 절단 품질과 톱날의 안전성을 향상시키기 위해 윤활제를 첨가 한 진자 톱으로 절단합니다.
우리는 밀링 머신의 바이스에“vise”의 세 가지 요소를 모두 클램핑하고 필요한 크기로 표면을 가공하며 위치가 변경 될 때마다 핸드 파일로 버를 제거합니다.



두 개의 공작물에서 나이프 블레이드를 잡고 고정하기위한 턱을 형성합니다. 이를 위해 각각의 크기는 한쪽에서 밀링됩니다. 세 번째 공작물은 양쪽에서 크기로 밀링됩니다. 턱으로 측면 그립을 고정하기위한 기초가됩니다.

가운데에있을 부분, 밀링 된 부분에서 세로 축에 대해 가장자리에 더 가깝고베이스에 약간 오프셋 된 두 개의 구멍을 표시합니다. 드릴링 머신에서 드릴합니다.
이 부품을 샘플로 사용하여 드릴과 얇은 드릴로 다른 두 블랭크의 응답 점을 표시하십시오.
그런 다음 직경이 큰 드릴로 표시된 지점을 얕은 깊이로 만듭니다 (우리는 둥지 종류를 만듭니다).
우리는 중앙 요소의 구멍에 같은 길이의 필요한 길이의 두 개의 핀을 꽂습니다.이 출력은 측면 요소를 설치할 때 홈에 들어가서 고정하지만 턱을 방해하지 않고 수렴하고 발산합니다.
기하학적 중심의 측면 턱 요소에서 동일한 직경의 구멍을 윤곽과 드릴로 만들고 손 탭으로 스레드를 자릅니다.
우리는 장치의 외관과 작동 용이성을 완성하기 위해 턱의 외부 가장자리를 밀링합니다. 또한 조의 조정을 방해하지 않도록 중앙 요소의 밀링 끝 양쪽에서 모따기를 제거합니다.

중심 요소의 바닥 중앙에서 맨드릴의 막힌 구멍을 개설하고 뚫습니다.

우리는 2 성분 접착제를 혼합하고 블라인드 홀에 필요한 길이의 맨드릴을 고정시킵니다. 화합물을 붙잡고 경화 시키십시오. 이를 위해 나무 바이스에서 맨드릴로 중앙 요소를 고정시킵니다.
우리는 선반 척에 계산 된 직경의 금속 막대를 고정하고 맨드릴의 직경보다 약간 큰 중심에 구멍을 뚫고 주기적으로 드릴링 영역에 그리스를 추가합니다.
그런 다음 약 10-12mm 높이의 실린더를 잘라 내고 측면에 구멍을 뚫은 다음 탭으로 나사를 조입니다.


외부의 측면 요소 중 하나에서 중앙 구멍을 뚫어 볼트 헤드 플러시를 설치하십시오.
마지막으로 우리는 분쇄기에서 에머리 끝없는 테이프로 처리 한 다음 낮잠 테이프로 처리하여 고정 장치의 표면을 마무리합니다.


연결 볼트를 조에 조이고 맨드릴에 원통형 링을 고정하여 잠금 나사로 올바른 위치에 설치하여 조정 가능한 홀더의 요소를 함께 조립해야합니다.
정착물 테스트
우리는 칼날을 홀더의 죠에 고정하고 원통형 링을 위 또는 아래로 움직여 필요한 경우 특수 나사로 고정하여 가로 막대의 필요한 높이와 맨드릴의 길이를 설정합니다.
샤프닝 각도가 블레이드의 전체 길이를 따라 동일하게 유지되기 위해서는, 전기 샤프너의 원의 전방에 수평으로 장착 된로드의 표면 위에서 맨드릴에 고정 된 원통형 링의 슬라이딩을 보장하는 것으로 충분하다.



장력이없는 짧은 샤프닝 후, 나이프는 필기 용지를 무게별로 쉽게 절단하여 탁월한 샤프닝을 확인합니다.



Share
Pin
Tweet
Send
Share
Send